Silicone wire
Silicone wire
Item Number:Silicone wire
- Model: Silicone Wire
- Size: 0 GA-36 Gauge
- Color: Transparent, black, green, red, yellow, white, Custom
- Insulation: Silicone/Rubber Silicone/Flame Retardant Silicone
- Shield: None
- Jacket: None
- Packing: 305m, 610m, 2000, 4000m, Custom
- OD: According to the standard/Custom
- Conductor Material: Tinned copper, silver plated copper, bare copper
- Drain wire: None
Environmental Specifications:
Environmental Space – Non-plenum
Flame Test Method – VW-1 FT-2
Installation Temperature – -40 °C to +250 °C
Operating Temperature – -40 °C to +250 °C
Temperature Rating – 200 °C / 250 °C
General Specifications:
Cable Type
High temperature Silicone wire
Cable Component Type
Silicone
Conductor Gauge, singles
0AWG-36AWG
Conductor Type, singles
Solid/Stranded Single Core Wire
Characteristics:
- High temperature Silicone products:
- Temperature resistance 250 degrees
- Oil resistance, acid, and alkali resistance
- Virtually eliminates skin irritation
- Color stable at elevated temperatures
- Suitable for UV, ozone, or moisture exposure
- Suited for liquid-immersed/High temperature applications
- Suitable for applications to -40°C~250°C
Silicone wire is a very good high temperature wire, Silicone material is very stable and fexible, It can be used in many harsh environments for a long time, and the wire made of silicone is thinner than the high temperature wire made of other materials.
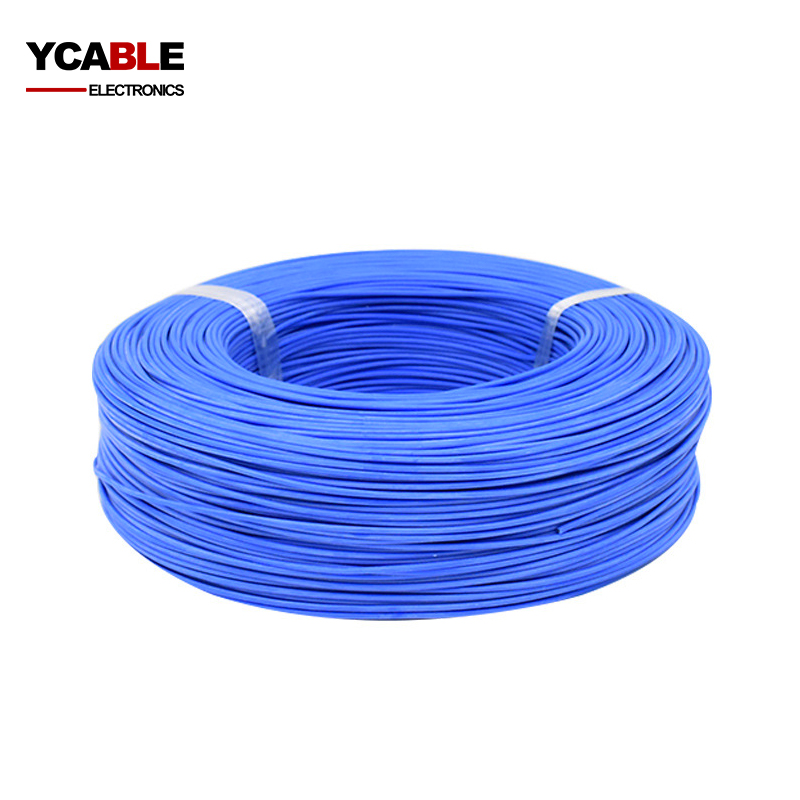
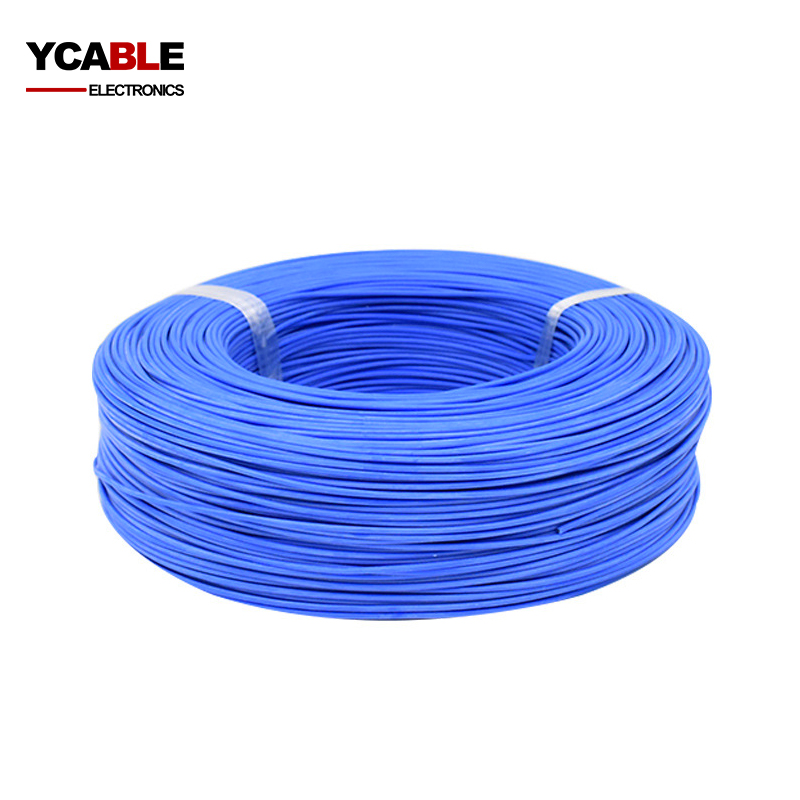
Categories
High Temperature Silicone Wire
Silicone Wire Specifications | |||||
AWG | Conductor structure number/wire diameter(mm) | Insulation thickness (mm) | Average outer diameter(mm) | Conductor DC resistance at 20 ℃ (Ω/km) | Package length (m) |
10 | 37 × 0.43 | 0.33 | 3.67 | 3.546 | 305 |
12 | 19 × 0.49 | 0.33 | 3.11 | 5.64 | 305 |
14 | 19 × 0.37 | 0.33 | 2.51 | 8.96 | 305 |
16 | 19 × 0.30 | 0.33 | 2.16 | 14.6 | 305 |
17 | 19 × 0.26 | 0.33 | 1.96 | 18.3 | 305 |
18 | 19 × 0.23 | 0.33 | 1.81 | 23.2 | 305 |
20 | 19 × 0.20 | 0.33 | 1.61 | 36.7 | 305 |
20 | 1 × 0.80 | 0.33 | 1.46 | 35.2 | 305 |
22 | 19 × 0.16 | 0.33 | 1.46 | 59.4 | 610 |
22 | 1 × 0.65 | 0.33 | 1.31 | 56.4 | 610 |
24 | 7 × 0.20 | 0.33 | 1.26 | 94.2 | 610 |
24 | 1 × 0.50 | 0.33 | 1.16 | 89.3 | 610 |
26 | 7 × 0.16 | 0.33 | 1.14 | 150 | 610 |
26 | 1 × 0.40 | 0.33 | 1.06 | 143 | 610 |
28 | 7 × 0.12 | 0.33 | 1.02 | 239 | 610 |
28 | 1 × 0.32 | 0.33 | 0.98 | 227 | 610 |
30 | 7 × 0.10 | 0.33 | 0.96 | 381 | 610 |
30 | 1 × 0.254 | 0.33 | 0.914 | 361 | 610 |
Description
What is silicone wire?
Silicone wire is renowned for its outstanding flexibility and user-friendly handling. The insulation, made from silicone, is notably soft and pliable, enabling the wire to be easily bent and flexed without the risk of cracking or breaking. This characteristic renders silicone wire a perfect option for scenarios requiring regular bending or movement, including uses in robotics, drones, DIY lithium battery pack construction, and automotive wiring. Moreover, silicone wire jackets are capable of enduring temperatures up to 200°C.
Silicone cables are highly beneficial in industrial contexts. They boast an impressively broad thermal range, functioning efficiently in temperatures as low as -90°C (-130°F) and as high as 200°C (392°F). This extensive thermal capacity makes them a top choice for applications sensitive to heat. Along with their thermal resilience, silicone cables are also celebrated for their pliability. Made from silicone, a material derived from a rare earth mineral, these cables naturally resist fire, making them among the most reliable options for heat-sensitive environments.
While silicone as a rubber material may not possess the mechanical robustness against impacts like harder materials, manufacturers have innovatively enhanced its durability by applying a silicone varnish. Despite this, the primary strength of silicone-insulated wire in both residential and commercial applications lies in its fire resistance. For situations where maintaining electrical circuit integrity is essential, silicone-insulated wires are unparalleled in reliability.
PVC vs Silicone Wire
Manufacturing Process
- Silicone, a synthetic rubber known as polysiloxane, is synthesized from silicon, hydrocarbons, and additional chemicals.
- PVC, or polyvinyl chloride, is a thermoplastic polymer created through the chlorination of hydrocarbon polymers, forming vinyl chloride monomer, and further modified with additives for versatility.
Material Resistance
- PVC stands out for its robust resistances, including acids, alkalis, UV, ozone, flames, and hydrocarbons, as well as grease, oil, and general weathering, making it a versatile choice for varied environments.
- Silicone, although not matching PVC's comprehensive resistance, excels in resilience against weather, UV, ozone, flames, and steam, with the potential for enhanced electrical conductivity via additives and low chemical reactivity.
Temperature Suitability
- Silicone is remarkable for handling extreme temperatures, enduring up to 480°F and as low as -60°F to -150°F, ideal for heat-intensive applications.
- PVC, though less adept in temperature extremes, functions in environments up to 140°F and down to 5°F.
Durability and Toughness
- PVC, available in both rigid and flexible forms, offers a broad range of hardness and enduring durability, resistant to corrosion and harsh conditions.
- Silicone, less durable inherently, can be fortified with fillers for enhanced strength and resilience, and offers notable compression recovery.
Cost Analysis
- PVC is generally more economical due to simpler production methods.
- Silicone, with a more complex manufacturing process, comes at a higher cost but may prove cost-effective for specialized applications where alternatives would not suffice.
In summary, the choice between silicone and PVC hinges on factors like manufacturing process, resistance needs, temperature requirements, durability, and cost-efficiency. While PVC is budget-friendly and versatile, silicone's unique properties make it indispensable for high-performance, specialized applications.
Silicone Rubber Insulation in Battery Cables
Silicone rubber stands out in battery cable insulation due to its unparalleled ability to endure vast temperature ranges, from -60C to +250°C, surpassing other materials like PVC and polyethylene. Elkem's silicone insulation is rigorously tested to maintain stability at temperatures up to 200°C for extended periods (3000 hours), catering to the diverse thermal demands of conventional motors and electric vehicle (EV) thermal management systems. This adaptability plays a crucial role in controlling battery temperature, optimizing heat transfer, and mitigating thermal runaway risks in EVs. Exceptional Flexibility:
Another significant advantage of silicone rubber for battery cables is its flexibility. This attribute is invaluable in the automotive industry, where Original Equipment Manufacturers (OEMs) and parts suppliers deal with complex wiring configurations in constrained engine spaces. Often, intricate shapes like U-bends or hairpin turns are needed to connect various engine components. The pliability of silicone insulation streamlines manufacturing processes and boosts overall efficiency.
In terms of weight, silicone insulation materials are considerably lighter compared to other high-temperature resistant materials. This weight reduction is crucial for energy conservation and lessening environmental impact across all automobile types. Particularly in EVs, the lightweight nature of silicone insulation contributes to greater vehicle autonomy, a key factor for consumer satisfaction.
Safety is another area where silicone insulation excels, thanks to its fire-retardant properties and unique ability to self-extinguish. This prevents flame spread in engine compartments, offering an elevated safety standard in automotive applications.
Silicone Wire vs Teflon Wire
Ease of Stripping:
- Silicone: The stripping process is more manageable with silicone rubber insulation. It does not require full cutting, reducing the risk of damaging the conductor.
- Teflon: Teflon's tough insulation nature makes the stripping process more laborious, posing a higher risk of conductor damage.
Flexibility:
- Silicone: Demonstrates superior flexibility at room temperature, which it preserves even under temperatures below 100 degrees Fahrenheit, making it easier to handle.
- Teflon: Generally stiffer, Teflon decreases the flexibility of the insulated conductors, making handling more challenging, although it retains some flexibility below 100 degrees Fahrenheit.
Solderability:
- Both silicone rubber and Teflon withstand high temperatures during soldering, unlike typical low melting point thermoplastics. This characteristic is crucial for wiring complex control panels, preventing damage to adjacent installations due to a soldering iron's accidental contact.
Summarizing, silicone and Teflon both offer unique advantages for wire and cable insulation under high-temperature conditions. Silicone’s ease of handling and flexibility make it a more user-friendly option, while Teflon’s durability offers long-term resilience, albeit with more difficult handling. The choice between them largely depends on the specific requirements of the application, considering factors like ease of installation, handling demands, and the operating environment.
Service Temperature Range:
- Both Teflon and silicone wires excel in the -100 to 500 degrees Fahrenheit range. While both demonstrate high-temperature stability, silicone rubber tends to harden and shrink under prolonged high temperatures. Teflon, on the other hand, decomposes at extreme temperatures, releasing fluorine-containing compounds, necessitating adequate ventilation above 400 degrees Fahrenheit.
Overload Reliability:
- Under overload conditions, Teflon insulation may decompose and emit toxic fumes. Silicone wires might become brittle, but an outer glass braid can preserve their insulating properties.
Flame Resistance:
- Silicone wires are slow to burn, producing mostly silicone dioxide ash, a good dielectric. Teflon is non-flammable but decomposes in direct flame, releasing toxic fumes.
Cold Flow:
- Teflon is prone to deformation under pressure due to its plastic nature, with some permanent deformation. Silicone wires, being elastomeric, exhibit minimal cold flow.
Cut-through Resistance:
- Teflon shows higher resistance in the thumbnail test than silicone but is susceptible to loosening due to its low cold flow resistance. Modern silicone wires are robust enough to resist lacing cut-through and don’t promote loosening.
Electrical Characteristics:
Fundamental Properties:
- Teflon wires have exceptional electrical stability, ideal for high-frequency applications.
- Silicone rubber’s electrical properties vary, but electrical grade compounds excel in volume resistivity, dielectric strength, and power factor.
Dielectric Fatigue:
- Short-term, Teflon outperforms silicone in dielectric strength. However, Teflon is prone to dielectric fatigue under prolonged moderate electric stress, unlike silicone.
Arc Resistance:
- Both materials have good arc resistance, withstanding over 200 seconds in standard tests without forming a carbon path.
Corona Resistance:
- Silicone exhibits excellent corona resistance, rivaling mica, while Teflon, like other organics, erodes under corona effects.
Application Specifics:
- Teflon Wiring: Ideal for high-temperature, military, and general hook-up applications, Teflon wires are favored for their durability and ability to withstand temperatures up to 450 degrees Celsius. They are commonly used in robotics, automation, navigation, air conditioning, and automotive applications.
- Silicone Wiring: Known for its insulation and high-temperature flexibility, silicone wires are suitable for hook-up wiring in high-temperature environments, fitting into compact spaces and enduring moderate handling.
Conclusion: Choosing Between Silicone and Teflon Wires Ultimately, the choice between silicone and Teflon wires depends on the specific requirements of the application. Each type offers distinct advantages and limitations, making neither universally superior. It’s important to consider the application’s needs to determine the most appropriate wire type.