Custom Cable Assemblies / Harnesses
Custom Designs (OEM/ODM)
YCABLE ELECTRONICS offer many kinds customized or OEM cables and wires in different fields.
Our Capabilities

ENGINEERING TEAM:
Our engineering team consists of production engineer, electronic engineer and mechanical engineer. Each engineer is very professional and dedicated.
New product design and development:
YCABLE ELECTRONICS can design different products for you according to your needs in different fields. Our current design productions includes:
1. Cable Assemblies and Wire Harnesses(Kiosk wire harness for parking lot automation/Automotive cables/Deutsch 9P and 6P to HD26P/OBDII to Atari 14P/Waterproofed USB cable/Audio cables/New energy vehicles cable...)
2. Ultrasonic welding products(PCBA Assembly/Ultrasonic welding/ Assembly cover/PCBA assembly molding...).
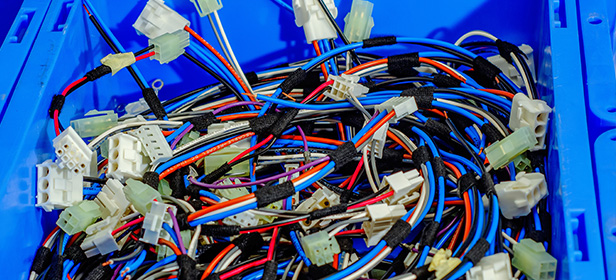
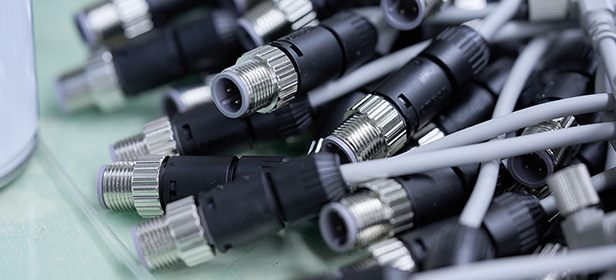
REVERSE ENGINEER:
Step 1 Get samples.
Step 2 Material analysis.
Step 3 Electrical/physical performance analysis
Step 2 Drawing the 2D & 3D drawing sheet according to the samples
Step 4 Make quotations
Step 5 Sample producing
2D&3D DESIGN:
We provide two types of drawings, 2D and 3D, to determine the specification details of the product and provide a more intuitive understanding of the product structure, which is helpful for product development and specification confirmation.
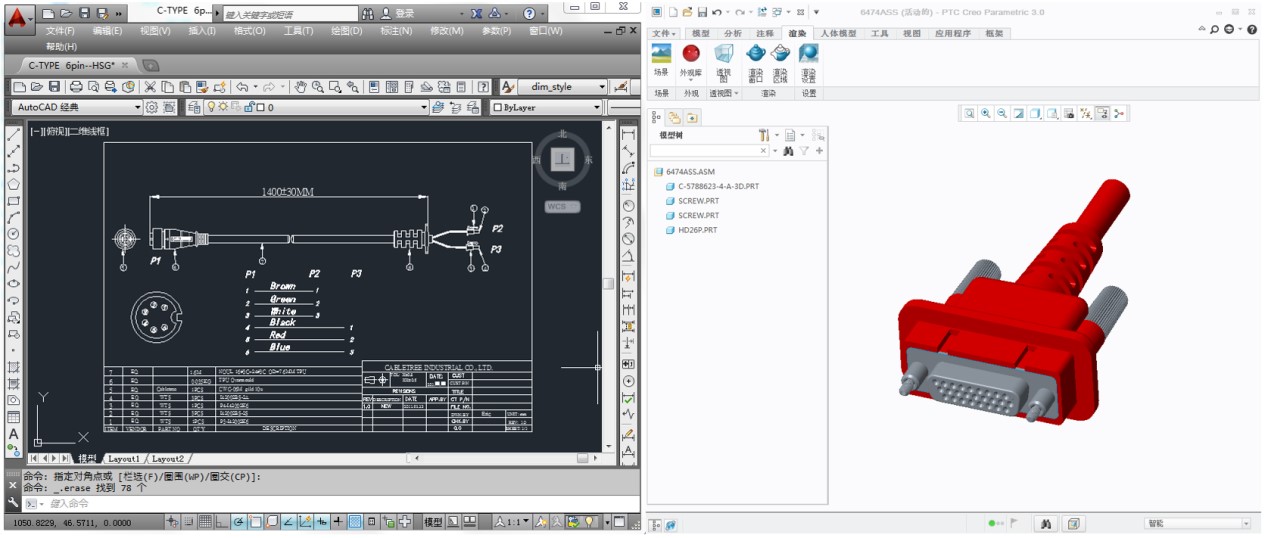
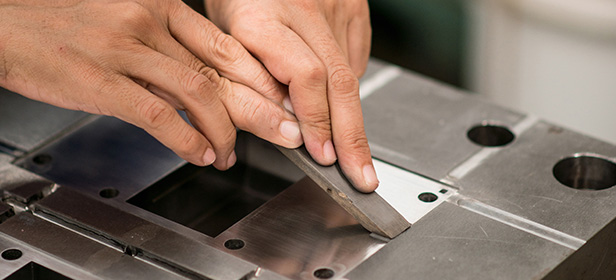
Design and development of molds:
After confirming the specifications, we will design molds for the injection molding part, After the preliminary mold is made, we will make a preliminary attempt and conduct testing after completing a sample. We will make electrical performance tests on internal connections, waterproof tests on overall components, and visual inspections and so on.
E-LAB:
1. PCB mock up
2. Signal Generator
3. Bridge Test
4. Oscilloscope
5. Frequency Meter
6. Quadratic Element Analysis
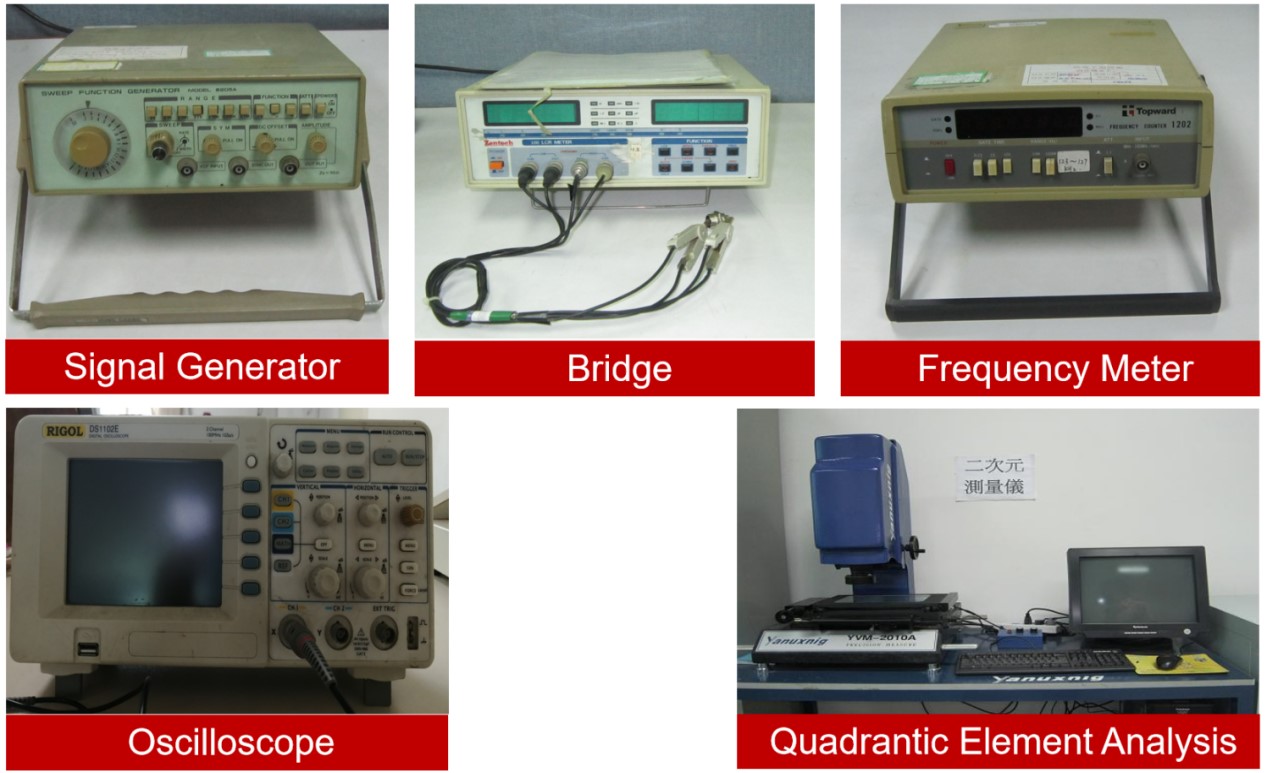
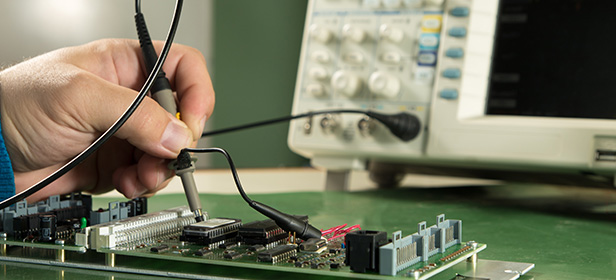
Reliability Test:
Electric: Insulation Test; Current Resistance Test; CIRRIS Tester; CT-8681 Tester; CT-8751 NAC Tester
Mechanical: Bending Test; Plug & Pull Force Test; Plug & Play Test (durability test); 360°Rotation Test; Drop Ball Test; Torsion Test; Vehicle Standard Bend Test; Vehicle Standard Bend Test to SR with 5 Pounds Weight
Environment: High & Low Temp Test; High Temp Aging Test; Brine Spray Test; Ultraviolet Accelerated Aging Test
Case Analysis of Wire Harness&Cable Assembly Process Flow
Ycable Electronics is the leader in supplying high-quality wire harness and cable assembly.
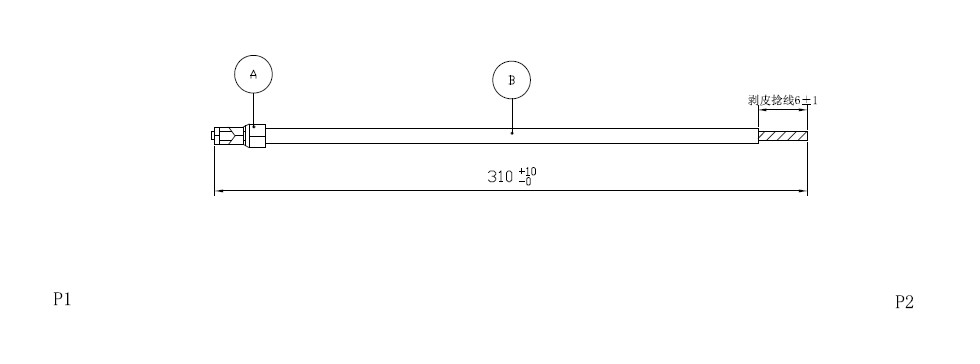
CASE A
The manufacturing process of this wire harness is:
- Cutting electrical wires to 310mm (computer cutting machine cuts electronic wires and peels both ends)
- Twisting (P2 end core wire twisting)
- Terminal punching (P1 end riveting terminal)
- Inspection (finished product inspection
- Packing
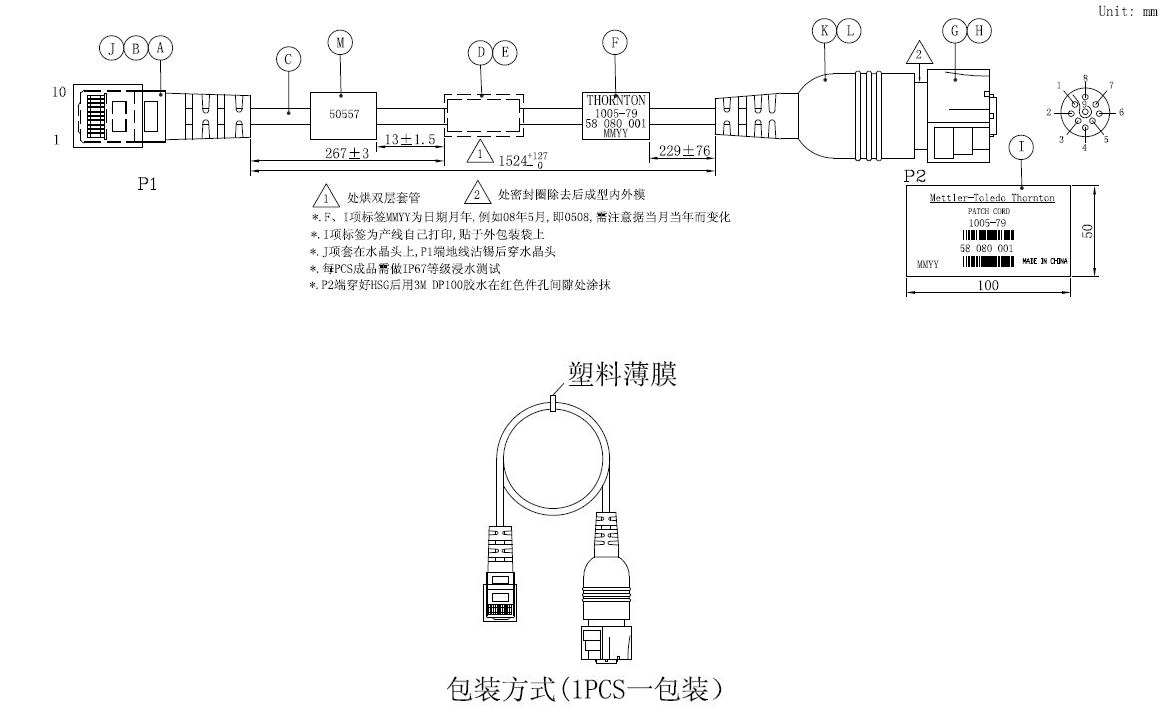
CASE B
The manufacturing process of this cable assembly is:
- Cut the CABLE length to 1524mm (manually cut with a cutter).
- Cutting the tube(Cutting by casing machine).
- Stripping the jacket both end of the cable.
- Stripping the insulation of the core wires and tinned(P2).
- Add the terminal (P2 end core wire riveted waterproof terminal).
- Terminal inspection.
- Threading through the tube (threading D and E casing from P1 end).
- Add the TELEPHONE JACK by hand, and fix it.
- Dismantle the waterproof terminal of item G.
- Thread the waterproof terminal (insert the P2 terminal into the waterproof terminal).
- Assemble the waterproof terminal (reassemble the previously disassembled components).
- Test the waterproof terminal assembly.
- Remove the waterproof head and apply glue.
- MOLDING the inner mold(P2).
- P2 end waterproof terminal immersion and air blowing inspection.
- Cable assembly continuity test
- MOLDING the outside mold(P2).
- IP67 immersion waterproofing test.
- Heating the tube.
- Dust cover (P1 end TELEPHONE JACK dust cover protection).
- Finished product inspection.
- Labeling
- Packing