PTFE wire
PTFE wire
Item Number:PTFE wire
- Model: PTFE Teflon Insulated Wire
- Size: 0AWG-36AWG
- Color: White/Blue/Black/Gray/Custom
- Insulation: PTFE/Teflon
- Shield: Unshielded
- Jacket: None
- Packing: 100M, 305M, 610M and OEM
- OD: -
- Conductor Material: Bare Copper, Silver plated copper, Nickel plated copper
- Drain wire: None
Environmental Specifications:
Environmental Space – Non-plenum
Flame Test Method – VW-1 FT-2
Installation Temperature – -40 °C to +250 °C
Operating Temperature – -40 °C to +250 °C
Temperature Rating – 200 °C / 250 °C
General Specifications:
Cable Type
High temperature PTFE Teflon wire
Cable Component Type
PTFE
Conductor Gauge, singles
0AWG-36AWG
Conductor Type, singles
Solid/Stranded Single Core Wire
Characteristics:
- High temperature PTFE Tefon products:
- Temperature resistance 250/260 degrees
- Oil resistance, acid, and alkali resistance
- Virtually eliminates skin irritation
- Color stable at elevated temperatures
- Suitable for UV, ozone, or moisture exposure
- Suited for liquid-immersed/High temperature applications
- Suitable for applications to -40°C~260°C
PTFE wire is a very good high temperature Teflon wire, PTFE Teflon material is very stable, It can be used in many harsh environments for a long time, and the wire made of Teflon is thinner than the high temperature wire made of other materials.
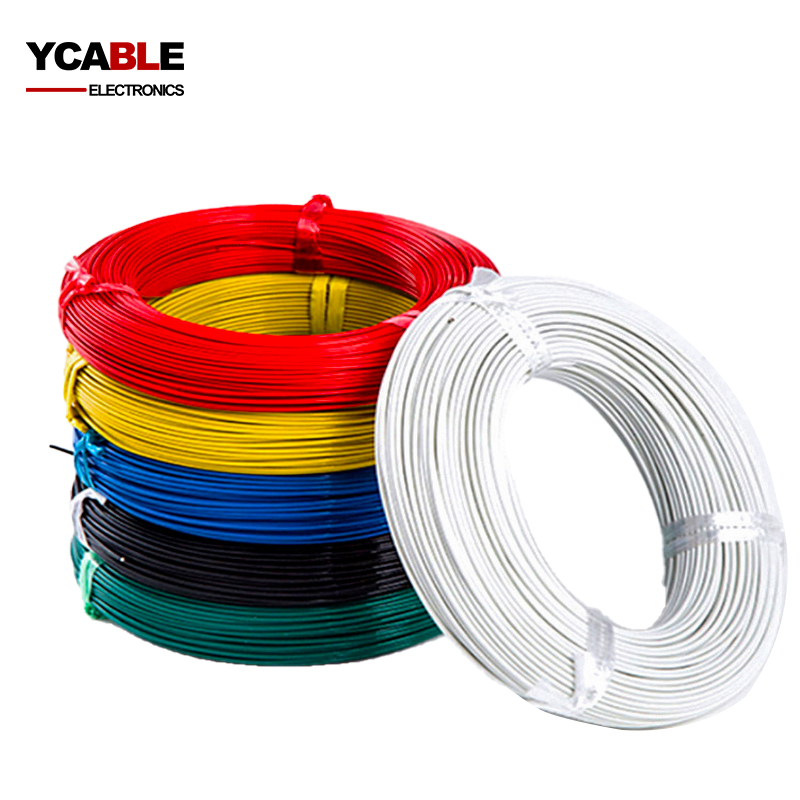
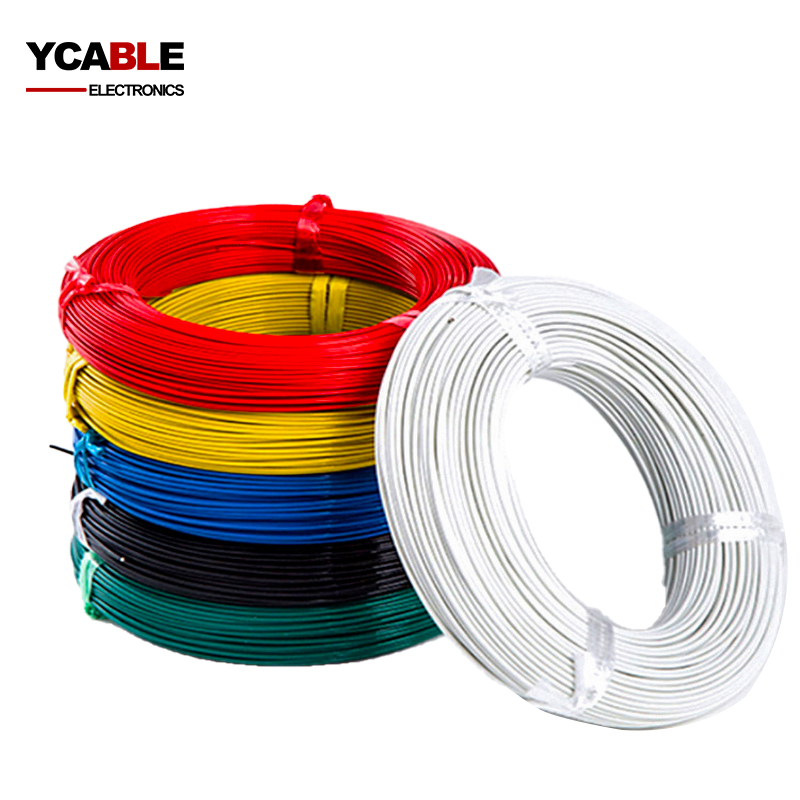
Categories
PTFE Teflon Insulatied Wire
PTFE Wire Pecifications | |||||
AWG | Conductor structure number/wire diameter(mm) | Insulation thickness (mm) | Average outer diameter(mm) | Conductor DC resistance at 20 ℃ (Ω/km) | Package length (m) |
10 | 37 × 0.43 | 0.33 | 3.67 | 3.546 | 305 |
12 | 19 × 0.49 | 0.33 | 3.11 | 5.64 | 305 |
14 | 19 × 0.37 | 0.33 | 2.51 | 8.96 | 305 |
16 | 19 × 0.30 | 0.33 | 2.16 | 14.6 | 305 |
17 | 19 × 0.26 | 0.33 | 1.96 | 18.3 | 305 |
18 | 19 × 0.23 | 0.33 | 1.81 | 23.2 | 305 |
20 | 19 × 0.20 | 0.33 | 1.61 | 36.7 | 305 |
20 | 1 × 0.80 | 0.33 | 1.46 | 35.2 | 305 |
22 | 19 × 0.16 | 0.33 | 1.46 | 59.4 | 610 |
22 | 1 × 0.65 | 0.33 | 1.31 | 56.4 | 610 |
24 | 7 × 0.20 | 0.33 | 1.26 | 94.2 | 610 |
24 | 1 × 0.50 | 0.33 | 1.16 | 89.3 | 610 |
26 | 7 × 0.16 | 0.33 | 1.14 | 150 | 610 |
26 | 1 × 0.40 | 0.33 | 1.06 | 143 | 610 |
28 | 7 × 0.12 | 0.33 | 1.02 | 239 | 610 |
28 | 1 × 0.32 | 0.33 | 0.98 | 227 | 610 |
30 | 7 × 0.10 | 0.33 | 0.96 | 381 | 610 |
30 | 1 × 0.254 | 0.33 | 0.914 | 361 | 610 |
Description
What is PTFE wire?
Superior PTFE Wire(we also call it Teflon wire), a manifestation of Polytetrafluoroethylene (PTFE) insulation, excels in rigorous environments. This fluorocarbon polymer, a Teflon wire variant, demonstrates remarkable resilience to fuels and lubricants, boasting both flexibility and exceptional thermal and electrical characteristics.
- Delving into PTFE's Essence: This Fluoropolymer, a derivative of tetrafluoroethylene, is known under numerous aliases. Its original patent in 1941 and trademark in 1945 have not altered its fundamental chemistry. PTFE, irrespective of its alias, retains its distinct properties.
- Curing Process and Efficiency of PTFE: Properly cured PTFE forms an insulation capable of enduring temperatures ranging from -90ºC to +260ºC. Its chemical inertness, resistance to atmospheric elements, non-flammability, and zero moisture uptake, position PTFE as a versatile material for diverse applications.
- PTFE's Role in Electronics: The insulating and mechanical prowess of PTFE is a boon in electronic components, beneficial to both PTFE wire manufacturers and users. It ensures products are safeguarded against heat, shock, chemical degradation, abrasion, and moisture.
- About PTFE Coated Wire: The PTFE coated wire effectively insulates micro miniature wiring, which often encounters corrosive agents that could deteriorate other materials.
- Frictional Properties of PTFE: PTFE's exceptionally low friction coefficient makes it ideal for high-friction, high-abrasion applications, like in bearings and gears.
- Chemical Robustness of PTFE Insulation: Chemically inert, PTFE insulation stands up to most chemicals, oils, alkalis, and moisture. It's non-toxic, mold and mildew resistant. Its flexibility, coupled with a smooth, low-friction surface, simplifies installation in challenging areas. PTFE sustains its properties at elevated temperatures, with a melting point of 327 degrees Celsius, and is compatible with immersion in substances like oil, water, and gasoline.
PTFE, a material synonymous with versatility, is extensively utilized in a variety of demanding settings. Commonly, it forms the insulating and protective layers of cables.
Key Applications of PTFE in Wire and Cable Manufacturing
PTFE Coaxial Cables: PTFE shines here due to its high temperature endurance, enabling the transmission of high power. Its robust electrical characteristics lead to minimal loss during high-frequency signal transmission.
PTFE Insulated Wires: Frequently chosen for environments demanding high-temperature tolerance and chemical resistance. Ideal for use in sensors, automotive components, and chemical containers.
Aerospace Applications: Favored for its exceptional performance under low-temperature conditions.
Prominent Industries Benefitting from PTFE Wires:
- Military Industry: Relies on PTFE's durability and resistance in critical applications.
- Aerospace Industry: Utilizes PTFE for its reliability under extreme conditions.
- Oil and Gas Industry: Depends on PTFE's chemical and temperature resilience.
- OEM Appliance Wiring: Prefers PTFE for its adaptability and safety features.
- Coaxial Communications: Values PTFE for its superior signal transmission capabilities.
At YCABLE ELECTRONICS, our PTFE offerings include extruded materials, prominently featured in our coaxial cable lineup. We also produce tape-wrapped, heat-sintered PTFE, accommodating larger dimensions and sheathings as seen in our signal cables, where PTFE is used for both cores and outer layers.
What is the difference between PTFE and PVC wire?
Contrasting PTFE with PVC-insulated wires, PTFE insulation stands out for its chemical inertness, impervious to a vast array of chemicals, oils, alkalis, and moisture. This non-toxic material resists mold and mildew, boasts remarkable flexibility, and its smooth, low-friction surface aids in installations within conduits and hard-to-access areas. PTFE maintains its integrity at high temperatures without degrading or becoming brittle, withstanding up to 327 degrees Celsius. PTFE cables are also compatible with immersion in oil, water, or gasoline.
PVC and Teflon, while sharing attributes like durability, flexibility, and resistance to chemicals and UV radiation, diverge in their applications due to distinct properties.
- Insulating Layer Thickness: Teflon insulation in electronic wires is notably thinner compared to PVC. However, thickness does not directly correlate with insulation quality. Both materials vary in voltage withstand capabilities. For instance, in multi-strand wires, Teflon's advantage is its ability to remain thin while ensuring electrical performance.
- Temperature and Cold Resistance: Teflon excels in heat resistance, suitable for temperatures ranging from 105-250 degrees, whereas PVC is generally rated for 60-105 degrees. In military products operating around 65 degrees, Teflon is preferred as PVC insulation may degrade quickly at elevated temperatures, affecting device functionality.
- Flame Resistance: Teflon boasts superior flame resistance and is not easily ignitable, unlike PVC, which is more prone to catching fire. This difference is crucial for equipment safety.
- Appearance: Visually, PVC and Teflon wires differ in sheen; PVC has a duller finish, whereas Teflon appears glossier. This distinction aids in practical identification.
- Friction and Corrosion Resistance: Teflon wires offer enhanced resistance to friction and corrosion. This is particularly advantageous in scenarios where wires are subject to movement or exposure, like connections between different components that require sliding.
- Pressure Resistance: Teflon's pressure resistance is somewhat inferior to that of PVC wire.
- Use as Insulation or Sheath: PVC is versatile, being used for both insulation and sheathing. In contrast, Teflon is predominantly used for insulation purposes.
PTFE vs PFA vs FEP wire, what is the difference?
PTFE, FEP, and PFA stand as the most recognized fluoroplastics, each distinct in their attributes. Let's explore the uniqueness of these fluoropolymers and determine which is most suitable for specific applications.
Distinctive Traits of Fluoroplastics Fluoropolymers are renowned for qualities ideal for applications in medical, automotive, electrical, and domestic fields. They are characterized by:
- Exceptional tolerance to high temperatures.
- Non-stick surfaces.
- Surfaces with low friction.
- Robust resistance to chemicals and solvents.
- High electrical resistance. Each type of fluoroplastic has subtle variances, such as different temperature ranges, making them fit for various applications. When selected appropriately, fluoropolymers offer advantageous cost and performance ratios.
Advantages of PTFE wire PTFE, or Polytetrafluoroethylene, known as the forerunner among fluoroplastics, was discovered in 1938 by Roy J. Plunkett. It stands out as the most distinctive fluoropolymer, offering the best in temperature endurance, chemical resistance, and non-stick properties. PTFE's unique advantages include:
- Optimal balance of cost and performance.
- Highest continuous operational temperature among fluoroplastics (+260°C).
- Almost universal resistance to chemicals.
- Exceptionally non-stick.
- Translucent appearance. However, PTFE's non-melting nature when heated makes processing challenging, requiring specialized methods for molding, extruding, and welding. Its exceptional properties make PTFE ideal for electrical insulation and safeguarding electronic components.
Benefits of FEP wire FEP, or Fluoroethylenepropylene, is a variant of PTFE that can be melted and processed. Similar to PTFE in properties, FEP's maximum operational temperature is +200°C. FEP's moldability and weldability allow for complex shapes. FEP's advantages are:
- Capability for welding and remolding.
- Operational temperature range of -200°C to +200°C, maintaining flexibility in cryogenic temperatures.
- Complete resistance to chemicals and UV light.
- Biocompatibility.
- Clear color. With these attributes, FEP is perfect for encapsulating sensitive electrical components, thanks to its low shrink temperature that prevents damage to temperature-sensitive materials.
Advantages of PFA wire PFA, or Perfluoralkoxy, is a high-temperature variant of FEP. Similar to FEP but usable at up to +260°C while remaining melt-processable, PFA has a lower melt viscosity than PTFE. Key benefits of PFA include:
- Continuous operational temperature of +260°C, the highest among fluoroplastics.
- Potential for welding and remolding.
- Effective permeability resistance.
- Superior chemical resistance, even at elevated temperatures.
- Biocompatibility.
- Availability in high purity grades.
- Clear color. PFA's primary disadvantage is its higher cost compared to PTFE and FEP. It is extensively used in high-purity, high-temperature, and chemical-resistant applications, such as medical tubing, heat exchangers, semiconductor components, pumps, and valve liners.
Custom PTFE wire manufacturer in China
For clients requiring wire that is both flexible and capable of withstanding high temperatures, our tailored PTFE wire production is the ideal solution. Leveraging years of experience collaborating with businesses like yours, we understand your specific application needs and requirements. Our approach goes beyond mere manufacturing; we craft tailored solutions, recognizing that each application is unique. This results in both standard and custom PTFE wires that effectively meet your specific objectives.
PTFE Wires for Diverse Applications Years of refinement in our production process have enabled us to offer optimized PTFE wire solutions. Whether for industrial, communication, energy, transportation, or consumer electronic applications, our PTFE coated wires are designed to suit your needs.
Specialization in PTFE Wire and Cable Our expertise extends to PTFE wire and cable ranging from AWG gauge 24 to 50, with PTFE insulation thicknesses from .00025'' to .006''. We utilize silver-plated copper wire and can incorporate other conductors like nickel-plated copper or bare copper to align with your application's requirements.
Wide Range of Wire Applications Our PTFE wires find applications in various sectors including medical, aerospace, electronics, communications, and more.
Features of Our Wires
- Enhanced flexibility for diverse uses
- Availability in long lengths
- Variety of color options
- Chemical inertness
- Multilayer TFE insulation for added durability
- Multiple configuration options
- Standard feature of silver-plated conductors, with other choices available
- Operating temperature range from -90°C to 260°C
For all your needs related to PTFE cables and wires, whether standard or miniature sizes, our commitment is to provide solutions that facilitate your work. We cater to orders of any size with a focus on delivering solutions that meet your specific requirements. For further information or to discuss your needs, please feel free to contact us.