FEP wire
FEP wire
Item Number:FEP wire
- Model: High temperature Teflon FEP wire
- Size: 0AWG ~ 36AWG
- Color: Transparent, red, black, green, yellow, gray, Custom
- Insulation: FEP 200℃
- Shield: none
- Jacket: FEP
- Packing: 305m, 610m, 1000m, 5000m, Custom
- OD: According to the standard/Custom
- Conductor Material: Tinned copper, silver plated copper, bare copper
- Drain wire: none
Environmental Specifications:
Environmental Space – Non-plenum
Flame Test Method – VW-1 FT-2
Installation Temperature – -40 °C to +250 °C
Operating Temperature – -40 °C to +250 °C
Temperature Rating – 200 °C / 250 °C
General Specifications:
Cable Type
High temperature FEP Teflon wire
Cable Component Type
FEP
Conductor Gauge, singles
0AWG-36AWG
Conductor Type, singles
Solid/Stranded Single Core Wire
Characteristics:
- High temperature FEP Tefon products:
- Temperature resistance 150/200/250 degrees
- Oil resistance, acid, and alkali resistance
- Virtually eliminates skin irritation
- Color stable at elevated temperatures
- Suitable for UV, ozone, or moisture exposure
- Suited for liquid-immersed/High temperature applications
- Suitable for applications to -40°C~250°C
FEP wire is a very good high temperature Teflon wire, Teflon material is very stable, It can be used in many harsh environments for a long time, and the wire made of FEP Teflon is thinner than the high temperature wire made of other materials.
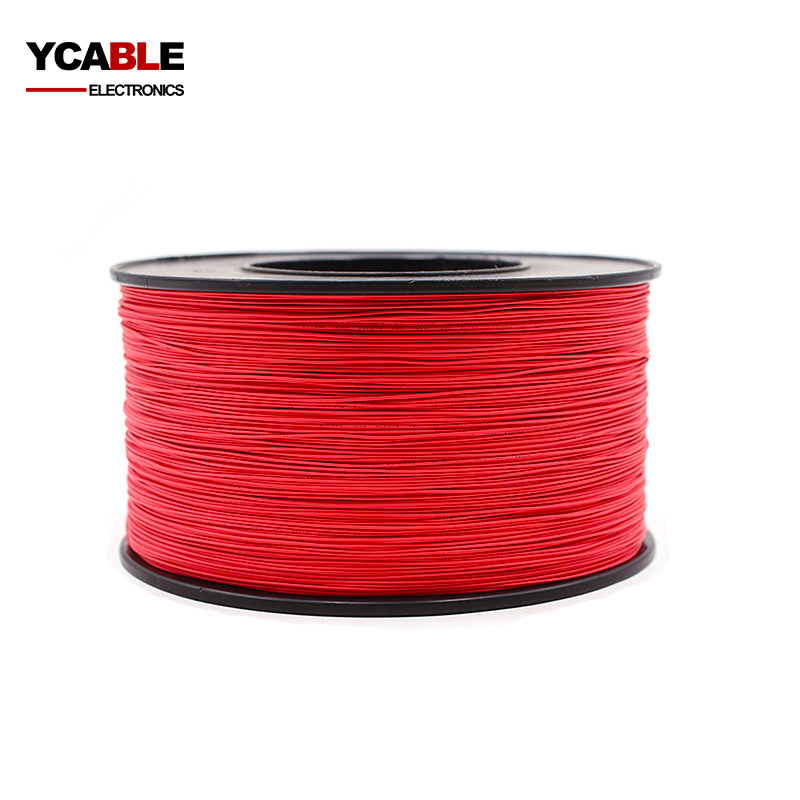
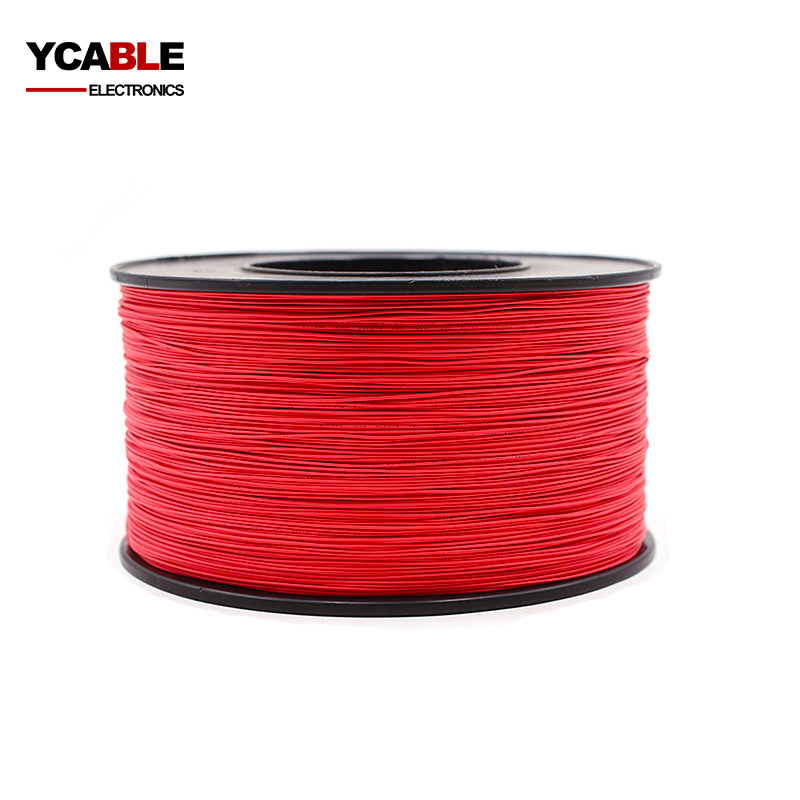
Categories
FEP Teflon Wire
FEP Wire Specifications | |||||
AWG | Conductor structure number/wire diameter(mm) | Insulation thickness (mm) | Average outer diameter(mm) | Conductor DC resistance at 20 ℃ (Ω/km) | Package length (m) |
10 | 37 × 0.43 | 0.33 | 3.67 | 3.546 | 305 |
12 | 19 × 0.49 | 0.33 | 3.11 | 5.64 | 305 |
14 | 19 × 0.37 | 0.33 | 2.51 | 8.96 | 305 |
16 | 19 × 0.30 | 0.33 | 2.16 | 14.6 | 305 |
17 | 19 × 0.26 | 0.33 | 1.96 | 18.3 | 305 |
18 | 19 × 0.23 | 0.33 | 1.81 | 23.2 | 305 |
20 | 19 × 0.20 | 0.33 | 1.61 | 36.7 | 305 |
20 | 1 × 0.80 | 0.33 | 1.46 | 35.2 | 305 |
22 | 19 × 0.16 | 0.33 | 1.46 | 59.4 | 610 |
22 | 1 × 0.65 | 0.33 | 1.31 | 56.4 | 610 |
24 | 7 × 0.20 | 0.33 | 1.26 | 94.2 | 610 |
24 | 1 × 0.50 | 0.33 | 1.16 | 89.3 | 610 |
26 | 7 × 0.16 | 0.33 | 1.14 | 150 | 610 |
26 | 1 × 0.40 | 0.33 | 1.06 | 143 | 610 |
28 | 7 × 0.12 | 0.33 | 1.02 | 239 | 610 |
28 | 1 × 0.32 | 0.33 | 0.98 | 227 | 610 |
30 | 7 × 0.10 | 0.33 | 0.96 | 381 | 610 |
30 | 1 × 0.254 | 0.33 | 0.914 | 361 | 610 |
Description
What is FEP wire?
FEP, or Fluorinated Ethylene Propylene, is renowned for its superior electrical qualities, wide temperature spectrum, and robust chemical resistance. FEP, a type of fluoropolymer, is frequently utilized as both insulation and jacket material in wire and cable production. Its ability to be foamed makes it an excellent dielectric in coaxial cables. Also known as Teflon® FEP, a variant of DuPont™'s Teflon®, this material is known for its exceptional resistance to chemicals, broad operational temperature range, and excellent electrical properties. These traits make FEP a preferred material across various industries, including aerospace, medical, lighting, and electronics. YCABLE ELECTRONICS offers specialized FEP cable solutions, featuring rapid production and minimal order requirements.
FEP is particularly favored in high-temperature plenum settings. It's also commonly used as insulation and filler in TEC cable within the oil and gas sector. In military applications, FEP is a key component in coaxial cables like M17/113-RG316, also known as RG316 coaxial cable.
As a fluoropolymer insulation, FEP stands out for its chemical resistance, extensive temperature range, and exemplary electrical properties. These characteristics render FEP an optimal choice for various sectors including chemical, medical, electronics, and aerospace industries.
Fluorinated Ethylene Propylene (FEP) cable wire is distinguished by its high voltage protection capabilities, stemming from FEP's remarkable dielectric properties. This results in FEP wires having smaller diameters compared to other high voltage alternatives. Additionally, FEP is characterized by its high resistance to stress cracking, maintaining toughness and flexibility even at elevated temperatures up to 200°C. This wire is notably resistant to various chemicals, including transformer oils, and features a low coefficient of friction. It also boasts low flammability, minimal moisture absorption, and excellent resistance to ozone, sunlight, and weathering.
FEP's role as a non-hygroscopic fluoropolymer makes it ideal for critical physiological and medical applications where small diameter, longevity in flex-life, and non-toxic insulation are crucial. It is specifically engineered for sustained use in devices such as flow probes and pressure measuring instruments, enduring extreme, repeated flexing at both high and low temperature ranges.
UL1330 and UL 1332 wires, falling under this category, are apt for internal wiring in appliances like ovens, as well as in automotive headlamps, mercury switches, computers, and motor leads. These wires are also suitable for immersion in gasoline and gasoline vapor, and can withstand temperatures of 80°C in oil environments.
Common Types of FEP Wire or Cable and Their Industry Applications Include:
- Aviation Wiring
- Aerospace Wiring
- Electronics Wiring
- Medical Wiring
- Appliance Wiring
- Lighting Industry Wiring
- Military Applications
- Oil and Gas Industry Wiring
- Chemical Industry Wiring
What are the advantages of FEP wire?
FEP, standing for Fluorinated Ethylene Propylene, is a versatile fluoropolymer/fluoroplastic, extensively used in cable sheathing and insulation. It is often aligned with PTFE and PFA cables, given its similar traits such as chemical inertness, notable dielectric strength, and an extensive temperature spectrum, though slightly less broad than its counterparts.
Owing to its physical and electrical characteristics, FEP is particularly advantageous in high-temperature sensor wire applications, promoting efficient power transmission with minimal signal loss. Consequently, FEP insulation or sheathing is frequently chosen in sectors like aviation, life sciences, oil and gas, petrochemical, and defense.
Key attributes of FEP sheathed cables encompass:
- A substantial operational temperature window, ranging from -40°C to +200°C.
- Exceptional resistance to both chemicals and UV radiation.
- Flexibility, along with the capacity for remolding.
- Non-stick surface and a low coefficient of friction.
- Enhanced durability, attributed to its low-friction properties.
PVC wire VS FEP wire
Choosing the right wire jacket often narrows down to deciding between FEP and PVC jackets, each distinct in their characteristics and price points. FEP wire, noticeably pricier than PVC wire, reflects the substantial differences in properties and applications between the two.
PVC, or polyvinyl chloride, also known as vinyl, is a prevalent jacket material in the market, primarily suited for low-voltage applications. In contrast, FEP is typically more appropriate for higher voltage applications. PVC jackets come in various types, each with different levels of pliability and electrical properties, leading to significant price variations. Common PVC types include:
- Standard PVC: Used mainly in commercial, industrial, and computer/control wire applications.
- Semi-Rigid PVC: Offers more toughness and stable electrical properties than standard PVC, providing enhanced protection.
- Indicated PVC: Known for its high abrasion resistance and is non-thermoplastic.
While PVC cables are durable and suitable for a broad temperature range, they are not recommended for use above seventy degrees Celsius due to limited thermal ratings, and their decomposition can release Hydrochloric Acid (HCI).
FEP, or Fluorinated Ethylene Propylene, surpasses PVC in electrical properties, temperature range, and chemical resistance, often labeled as high-temperature wire. Unlike PVC, FEP can withstand prolonged exposure to ultraviolet light. However, FEP is also not ideal for high-voltage applications. There are two types of FEP wire:
- TFE Wire Jackets: Can be manufactured in extended lengths due to the properties of the material.
- FEP Wire Jackets: Produced in continuous long lengths and can be color-coded for specific control applications.
Despite its higher cost, FEP offers numerous advantages in various applications. It is resistant to a wide array of chemicals, including acids, hydrocarbons, and solvents, is easily sterilizable, and has a low volumetric expansion characteristic. Moreover, FEP is more capable of enduring extreme temperature fluctuations compared to PVC jackets.
What is the difference between FEP wire and PTFE wire?
Fluoroethylenepropylene, commonly termed as FEP, represents a variant of PTFE that is moldable upon heating. Exhibiting characteristics akin to PTFE, FEP distinguishes itself with a slightly reduced thermal threshold, capping at about +200°C. This material, notable for its malleability, lends itself well to crafting intricate shapes through welding and reshaping processes.
In the realm of cable insulation, PTFE takes precedence in scenarios demanding heightened thermal resilience, outpacing FEP, particularly in mechanical contexts. Conversely, FEP Teflon wire, known for its pliability, holds an edge in fabrication ease. Both FEP and PTFE cables find extensive application in environments subject to elevated temperatures, such as automotive high-temperature zones, oven circuitry, and components like temperature sensors and switches.
FEP wire, bearing a softer composition, succumbs to heat at lower temperatures compared to its PTFE counterpart. This quality renders it less prevalent in culinary heat-intensive tasks. However, its resistance to ultraviolet rays elevates its utility in outdoor and weather-related applications, underscoring its significance in such domains. As a FEP wire manufacturer, the focus lies on harnessing these attributes to cater to a spectrum of industrial needs.